Manufacturers discuss challenges and opportunities during Manufacturing Month
Click to listen to the full segment on The Minnesota Business Podcast
(Segment starts at 13:10)
Here’s what the experts had to say
Throughout the month of October, we celebrate manufacturers. Manufacturers are a core tenet of our economy and contribute to Minnesota’s legacy of economic strength.
At this month's Manufacturers’ Summit, we spoke with industry leaders – we asked them what they’re facing, what’s driving them and how they are innovating. Some themes emerged: they’re powering through workforce challenges, they’re automating to increase productivity and employee retention, and they’re still reeling from the impacts of the last legislative session.
SPEAKERS INCLUDED:
- Robin Loftis, Director, Human Resources, Clow Stamping Company
- Tom Radovich, Managing Director, Sappi North America, Cloquet
- Mike Speetzen, CEO, Polaris
- Ross Widmoyer, President and CEO, Faribault Mill
Workforce
Employers have been plagued with workforce challenges for nearly a decade. It’s a complicated issue with no silver bullet solution.
Brooke Lee, CEO of Anchor Paper in St. Paul posed the question this way: “Can you guys talk about what strategies have been successful for you in doing that in, keeping and recruiting talent?”
According to Tom Radovich, Managing Director at Sappi North America in Cloquet, they’ve had success in partnering with area high schools to fill a specific need for electricians.
“We started looking at a dual training grant," said Radovich. "I met with some administrators at the local high school in Cloquet and told them that I wanted to partner with them and get some kids that had backgrounds and shop classes and stuff like that to sign up for the program. So they interviewed for these positions. They get 75% of their tuition paid for by going to a local secondary education.”
Employers often go directly to schools to break down misunderstandings about careers in manufacturing. This can help them understand the higher level of sophistication in this work and their earnings potential.
“It’s important for us as manufacturers to share how important it is for them to also do these types of trades," added Radovich "I educate some of the students at the high schools to tell them look, you can make $150,000 at our facility in these roles.”
Empowering employees is a tried-and-true method to build an office and business culture that fosters growth and retention.
We were fortunate during this year’s Manufacturers’ Summit to hear from Mike Speetzen, the CEO of Polaris. Among the many insights he shared, he talked about employee ownership at their company.
“…I’ll tell you what builds the culture is everybody owns the company," said Speetzen. "Employee stock ownership plans fell out of favor years and years ago. And we’ve had those moments where we’ve looked at it and said, is this really worth doing? It is worth doing every year, all the way down to the shop floor. People get stock in their account, they also get bonuses, the get profit share, which makes us unique to a lot of companies. And yes, it is expensive, but it is worth it.”
Mike Speetzen, the CEO of Polaris
In smaller communities, having a stellar reputation as an employer helps.
Robin Loftis, Director of Human Resources at Clow Stamping in Merrifield, explains:
“Clow Stamping is really fortunate that they have an excellent reputation in the community," said Loftis. "We have robust referral programs… They have friends there, they have family members that already work there. They’re a great resource and we take advantage of that as much as possible… The Brainerd Dispatch has a local award to the best manufacturing company and the best large company to work for. We’ve received that five years in a row.”
AUTOMATION
Automation is not a four-letter word. Trends in automation have helped ease the burden of lack of workers in manufacturing for years.
Jeffrey Hohn is the President and CEO of Massman Companies, a leading designer in automation equipment in Villard, Minnesota.
Massman creates automation solutions for other companies. They believe highly in the ability of these products to help elevate the employee experience, while increasing productivity. Hohn shared of an experience he had speaking to one such employee.
“He said, you know, I used to work in consumer products group. And my boss came out and he kept telling me, work harder, work faster. You’re not keeping up with the line. And you know what he did? He said, I threw my gloves…. Said you take a chance. He said, my boss made it about two minutes before he started sweating and couldn’t keep up with the line. I want to work on a machine. I don’t want to be a machine.”
Many manufacturers say that innovations in automation help ease the labor shortage. And with no end to this shortage in sight, many employers are looking to automation to increase productivity and curb the rising costs of labor as well.
But new technologies can also help improve employee safety and accuracy in the manufacturing process.
“If you’re that guy who has to palletize the 40-pound bag of dog food out of the pallet, it’s not if you’re going to have back strain, it’s when you’re going to have back strain because some of those positions are very challenging… We take and automate that whole thing, so that those pallets and those drums come in on a conveyance system… Not only do we find that there’s cost benefits, but there’s also benefits for us in terms of the workplace safety," said Hohn.
New laws and mandates
The final theme we heard from manufacturers at the Summit was how they’re trying to make sense of the plethora of new laws, mandates and regulations from last legislative session.
Among those is a bill that will mandate employers to offer 20 weeks of paid leave to all employees. More than 80 percent of Chamber member businesses already offer benefit packages – tailored specifically to their workforce.
Applying this one-size-fits-all plan to all employers and all employees will drastically change the way that benefits are run in our state.
Top of mind for businesses? Getting the work done in an already-tight labor market.
Ross Widmoyer, President and CEO of Faribault Mills in Faribault, shared about the impact on his workforce.
“We have a hundred employees and our, our process, our manufacturing process there are 20 plus unique steps that go into making one of our handcrafted blankets… in many cases, in each of those 21 steps, we have two, maybe even one person who knows how to run a particular machine… And I was talking to a friend of mine who is an employment attorney. He said, companies think about for the future, plan on staffing up by 20% based on how employees will leverage this new law, which for companies like ours… becomes a major, major challenge.”
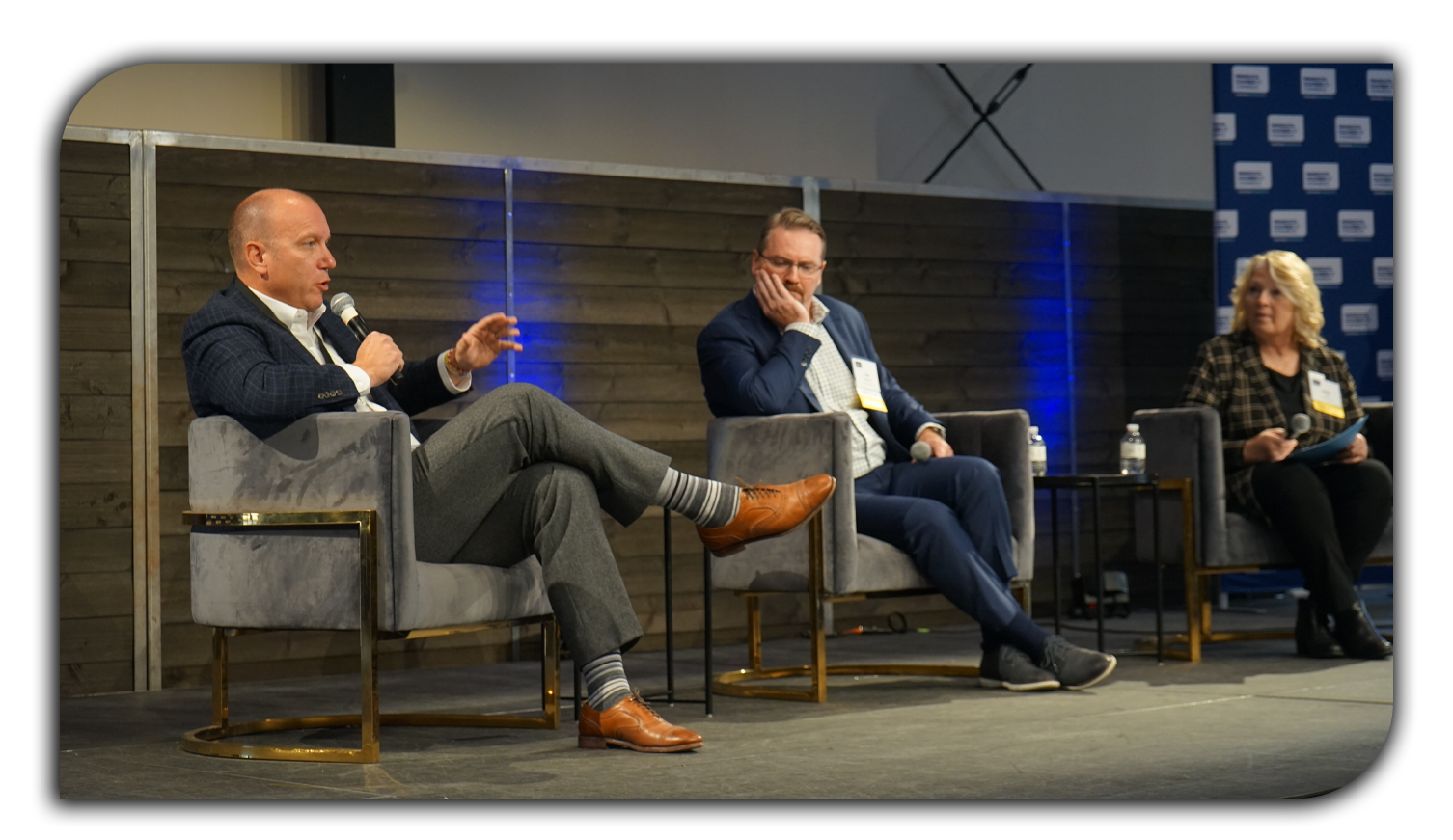
(From L-R) Ross Widmoyer, President and CEO of Faribault Mills, Tom Radovich, Managing Director at Sappi North America, Robin Loftis, Director of Human Resources at Clow Stamping
Ross isn’t alone in worrying about the staffing challenges – or the cost and complexity of compliance.
“You got two choices as a company," said Radovich. "Either you hire additional staff or people have to work more overtime. And that’s one of the things that I shared with politicians in our district, in and surrounding districts, is that you’ve already got people that went through COVID and had to work a lot of overtime, and now you’re just gonna make them that much more tired, regardless of how you feel about giving people time off. Most people in this room would agree that it’s important to give people time off. It’s just that companies do that on their own.”
We appreciate very much the pressures that our state’s manufacturers are under. They create jobs and quality of life in our communities.
At the Minnesota Chamber, we ask all of you to join us in celebrating the strength of this important industry throughout this month – and throughout the year. We are committed to providing a voice for manufacturers at the Capitol, so their ingenuity can continue to solve problems and usher our economy into the future.
Click below to listen to the full segment on The Minnesota Business Podcast
Segment starts at 13:10
Manufacturers' Summit attendee testimonial
"
Great structure of panels and speakers, and all those presenting were great. Great event for networking.
"
Interested in other Minnesota Chamber events?
Join us on November 16 for the 2023 Economic Summit!
Rising costs and interest rates, new technologies and a workforce shortage. How can we build on our legacy of economic strength and innovation, decipher this new world we are living in and build a better economy? At this signature event, you will have the unique opportunity to glean insights from an array of industry and political experts. Join us to gain valuable perspectives as Minnesota looks to enhance its economic future.